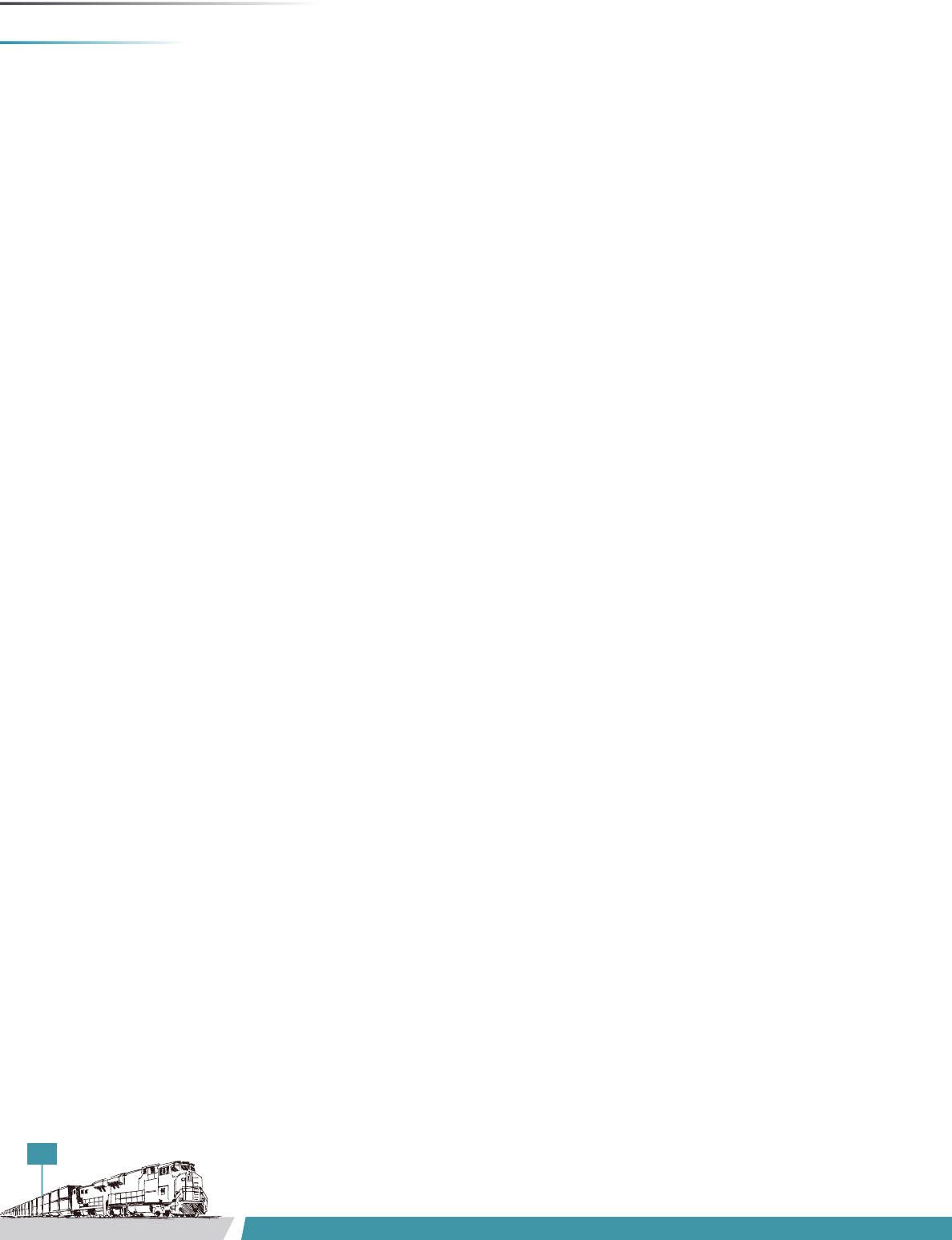
30
WORKING REPORT – FLY ASH
Opportunity of Fly-Ash Transport by
Rail
As discussed earlier also, the cement industry is likely
to be the main consumer of fly ash in the coming years.
Therefore, the report focusses on the possibilities of
transporting fly ash by rail from power plants to cement
plants. Presently, almost all fly-ash transportation
happens by road. The modal share of railways in
transportingyashwasonly2.3%in2016–17.Thermal
power plants generally construct silos for intermediate
storage of fly ash, from where it is transported to cement
plants either by bulkers or rail. Discussions with the
stakeholders from ACC Cement, NTPC, and the CMA
revealed that the major reasons for the use of road
transport are lower capital investment and complete
control over the transportation chain. These companies
have purchased road tankers and given them on labour
contract to agencies for provision of driver and other
manpower. They have also made capital investment at
both ends for the development of loading and unloading
facilities as well as the creation of silos for storage.
Some of these companies have entered into long-term
agreements with power plants for the supply of fly ash
(Nanduri, 2008). As the movement of y ash in road
tankers is expensive and unsuitable for large quantities,
several cement manufacturers have also located clinker-
grinding units close to the power plant.
To understand if it is feasible to transport fly ash by rail, it
is important to relate the patterns of fly-ash production
with the consumption centres, and also understand the
logistical requirements to move fly ash in bulk quantities.
Figure 7 shows that because coal-based power plants
are spread across the country, fly-ash generation is not
evenly distributed. Because of geographical advantage,
large coal-based plants are located in regions of Uttar
Pradesh, Jharkhand, Chhattisgarh, and West Bengal.
Other concentrations can be observed in Telangana and
the Telangana–Maharashtra border in the Wardha Valley
Coalfield. Some major power plants are also located
in Gujarat, Odisha, Bihar, and Andhra Pradesh. For a
better understanding these thermal power plants can
be divided into the following clusters throughout the
country:
Cluster 1: Five coal-based power plants with large
capacities are located in a cluster known as the Singrauli
region at the border of Uttar Pradesh and Madhya
Pradesh. These power plants are Obra, Rihand, Singrauli,
Anpara, and Vindhyachal. They have a combined fly-ash
generation of around 20 million tonnes per year. In the
same region, power plants with slightly lower capacities
are also located at Tanda, Panki, Unchahar, and Parichha.
Cluster 2: In Bihar and West Bengal, the major power
plants are Kahalgaon, Farakka, Mejia, and Kolaghat. The
power plants at Kahalgaon and Farakka alone produce
around 8 million tonnes of fly ash per year.
Cluster 3: In Chhattisgarh, the major power plants are
NTPC Sipat and Korba. Few other state-owned and
private sector plants like Jindal Thermal Power Plant and
others are also located in the same cluster. These power
plants produce around 15 million tonnes of fly ash per
year.
Cluster 4: In the Telangana, Andhra Pradesh, Karnataka,
and Maharashtra cluster, large coal-based power plants
are Ramagundam, Kothagudem, Vijayawada, Simhadri,
Rayalaseema, Raichur, Chandrapur, and Tirora. The
power plants at Ramagundam, Vijayawada, and Raichur
produce more than 10 million tonnes of fly ash per year.
Cluster 5: In the Gujarat and Rajasthan cluster,
Wanakbori, Ukai, Kota, JSW Barmer, and Suratgarh are the
major power plants which produce significant quantities
of fly ash in the western part of India.
Cluster 6: In the Delhi, Punjab, and Haryana cluster,
power plants located at Dadri, Jhajjar, and Hissar produce
significant quantities of fly ash.
Two case studies from the aforementioned clusters have
been selected and presented here to further understand
the various aspects involved in transporting fly ash by
rail and road.
Case Study I
Ramagundam Region
The southern region consisting of states like Telangana,
Andhra Pradesh, and Karnataka houses major power
plants like Ramagundam, Vijayawada, and Raichur, which
produce more than 10 million tonnes of fly ash per
year.In2007,aconcertedeffortwasmadebyRailways,